Forschungsprojekte
Bei Tiefbohrungen mit hohen Ansprüchen an die Bearbeitungsqualität, treten zu den Anforderungen an eine hohe Genauigkeit und Oberflächengüte auch zunehmend solche, welche die Bohrungsrandzone betreffen, also beispielsweise die Einhaltung eines definierten Eigenspannungszustands oder die Gewährleistung vorgegebener Gefügeeigenschaften. Um hier zuverlässig zu gewünschten Ergebnissen zu gelangen, werden der Bohrungsherstellung Autofrettage- oder Glatt- und Festwalzprozesse nachgelagert. Es wäre wünschenswert, definierte Bohrungseigenschaften schon im Verlauf der spanabhebenden Bohrungsbearbeitung so einzustellen, dass im Idealfall auf nachfolgende Bearbeitungsoperationen verzichtet werden kann.
Ziel des im Rahmen des Schwerpunktprogramms SPP 2086 „Oberflächenkonditionierung in Zerspanungsprozessen“ der DFG durchgeführten Forschungsprojekts ist es daher, Einflussgrößen im Ablauf des Bohrprozesses messtechnisch zu erfassen, um die Prozessbedingungen mittels eines Reglers gezielt verändern zu können und so die Eigenschaften der Bohrungsrandzone (z. B. Eigenspannungen, Härte und Rauheit) definiert zu beeinflussen.
Ein Teilziel des Forschungsprojekts betrifft die Entwicklung und Bereitstellung eines sensorintegrierten Werkzeugs, mit dem eine in-prozess-Erfassung des thermo-mechanischen Zustands in der Spanbildungszone sowie der auftretenden Werkzeugschwingungen möglich ist. Im Rahmen dieser Entwicklungen wird ein kombiniertes numerisch-analytisches Modell erstellt, mit dem von Sensordaten auf die tatsächlich wirkende Temperatur in der Wirkzone geschlossen werden kann.
Ein weiteres Teilziel betrifft die Entwicklung eines Zerspanungsmodells und eines Materialmodells, mit dem der Zusammenhang zwischen dem thermo-mechanischen Belastungszustand in der Spanbildungszone und den Eigenschaften der Bohrungsrandzone abgebildet und zeitunkritisch vorausberechnet werden kann. Die Ausgangsgrößen des Modells geben Auskunft darüber, welcher thermo-mechanische Zustand in der Wirkzone eingehalten werden muss, um zu gewünschten Randzoneneigenschaften zu gelangen. Ein weiteres, ebenfalls zu erstellendes analytisches, in-prozess-fähiges Modell ist Basis des eigentlichen Prozessreglers. Dieses Modell vergleicht die Ausgangsgrößen des Zerspan- und Materialmodells mit den Messdaten des sensorischen Werkzeugs und leitet aus der Bewertung der Abweichungen geeignete Stellgrößen ab.
Auf diesem Modell kann der Regler aufsetzten, der über eine geeignete Schnittstelle mit der Steuerung der Bearbeitungsmaschine kommuniziert und dieser Vorgaben zu Schnittdaten wie bspw. Schnittgeschwindigkeit oder Vorschub liefert um die Oberflächeneigenschaften der Bohrung gezielt einstellen zu können.
Im Umfang des Ad-Proc-Add-Projekts wird die additiv-subtraktive Fertigungsketten (ASM) untersucht. Ziel ist es ein detailliertes Verständnis der Abhängigkeiten und Wechselwirkungen von Material- und Bauteileigenschaften additiv gefertigter und überarbeiteter Werkstücke in Bezug auf die Prozessparameter, Fertigungsstrategien und Randbedingungen zu erhalten. Visionärer Bestandteil ist dabei, die Werkstückeigenschaften hinsichtlich Geometrie, Oberfläche und Untergrund über die ASM-Prozessketten hinweg so anzupassen, dass vordefinierte Anforderungen erfüllt werden können. Dies ermöglicht die gezielte Gestaltung und Implementierung von additiv-subtraktiven Produktionsketten in verschiedenen industriellen Anwendungen. Dazu wurde ein internationales Netzwerk von Forschungsverbänden und -instituten aufgebaut, in dem die notwendigen Kompetenzen in den Bereichen additive Fertigung, Zerspanungsprozesse, Prozessüberwachung und -steuerung, Maschinen und Anlagen, Simulation und Optimierung sowie Energieeffizienzanalyse gebündelt werden.
Umfangreiche experimentelle Untersuchungen zu Zusammenhängen zwischen Parametereinstellungen und Einflüssen auf die Werkstückeigenschaften in additiven und subtraktiven Prozessschritten, Korrelationsanalysen, die detaillierte Untersuchung physikalischer Effekte sowie Methoden zur Prozessüberwachung und Qualitätsprüfung sind in einem vernetzten Forschungsansatz umgesetzt, der Synergien und Kapazitäten der beteiligten Partner optimal nutzt.
Aus den Erkenntnissen dieses Projekts werden neue Werkzeugkonzepte, Strategien für den 3D-Druck von Metallteilen, Methoden für die anspruchsvolle Gestaltung von Nachbearbeitungsprozessen, Systemprototypen zur Überwachung von Geräten und Vorrichtungen sowie neue Dienstleistungen abgeleitet. Darüber hinaus ermöglicht das generierte Wissen Teilehersteller sowie System- und Dienstleistungsanbieter die Entwicklung neuer Produkte mit erweiterter Funktionalität. Zugleich ermöglicht es Endanwendern, ASM-Prozessketten mit höherer Produktivität und ökonomischer sowie ökologischer Effizienz zu realisieren.
Die Projektergebnisse werden zu einem digitalen Kompendium führen, das auf einem neuen Leistungsmesssystem basiert und für Konstruktions- und Produktionsingenieure sowie Servicemitarbeiter nutzbar ist. Begleitet wird das Projekt von einem Anwenderkomitee aus allen relevanten Marktsegmenten: Werkzeugbau, 3D-Druckanlagen, Werkzeugmaschinenbauer, Software- und Dienstleistungsanbieter sowie Endverbraucher. Die intensive Kommunikation mit den Industriepartnern gewährleistet die Erarbeitung von industriell relevanten und nutzbaren Ergebnissen.
In diesem Projekt geht es um die Potentiale für den Ersatz von Hartmetallschneidstoffen durch keramische Schneidstoffe bei der Herstellung von Sägewerkzeugen.
Ziel des Projekts war es, die Herstellung keramischer Schneidwerkzeuge am Beispiel von Sägewerkzeugen zu optimieren, um wirtschaftliche Alternativen zu Hartmetall-Schneidstoffen für den Massenmarkt bereitstellen zu können. Die wissenschaftliche Zielsetzung bestand in der Schaffung von Erkenntnissen zur Leistungsfähigkeit der Schneide im unterbrochenen Schnitt und der Auslegung von Prozessen zum Fügen- und Schleifen von keramischen Sägezähnen. Die gewonnen Erkenntnisse wurden auf konkrete Anwendungsfälle (Fräswerkzeuge, Kreis-, und Bandsägewerkzeuge) übertragen.
Die wesentlichen Projektergebnisse sind: Bei den wichtigsten Zerspanprozessen mit unterbrochenem Schnitt (bspw. das Sägen) hängt die erreichbare Standzeit von den wechselnden mechanischen und thermischen Belastungen sowie von der Geometrie und dem Verschleißverhalten des Werkzeugs ab. Aus diesem Grund wurde ein Modellprozess auf der Basis des klassischen Einstechdrehens ausgearbeitet, mit dem sich die Bedingungen des Kreissägens abbilden und Schneidstoffe vergleichend bewerten lassen. Die Werkstückkörper sind so ausgelegt, dass die Belastung eines Zahns im Sägeprozess nachgebildet werden kann. In Bild 1 sind sowohl der Aufbau des Modellversuchs in der verwendeten Drehmaschine (Gildemeister CTX 420 linear) sowie ein exemplarischer Werkstückkörper aus dem Baustahl S355JR dargestellt.
Im Projekt wurden neben dem Baustahl S355 auch Untersuchungen mit Grauguss GG25 und GGG60 sowie Aluminium EN-AW-7075 durchgeführt. Für die Qualifizierung im unterbrochenen Schnitt wurden Keramik-Einstechplatten aus Oxid- (SN 60), Nichtoxid-(Beta-Si3N4) und Mischkeramik (Alpha/Beta-SiAlON) eingesetzt. Als Referenzwerkzeug wurden Einstechplatten aus Hartmetall MG 12 mit gleicher Einstechbreite betrachtet.
Es konnte gezeigt werden, dass der entwickelte Modellversuch für eine schnelle und kostengünstige Qualifizierung von keramischen Schneidstoffen sowie Optimierung (Auslegung) der Schneidengeometrie im unterbrochenen Schnitt gut geeignet ist. Die ermittelten Ergebnisse zeigen dabei für die Nichtoxid- und Mischkeramiken ein hohes Potenzial für die Bearbeitung von Gusseisen GG25 im unterbrochenen Schnitt. Die beiden keramischen Schneidstoffe könnten damit in diesem konkreten Bearbeitungsfall zur Substitution von Hartmetall herangezogen werden.
Das Projekt wurde unter Beteiligung des Fraunhofer IPA und des KSF der Hochschule Furtwangen sowie mehrerer Indurstrieunternehmen durchgeführt.
Gefördert durch: Ministerium für Finanzen und Wirtschaft Baden-Württemberg
Entwicklung einer adaptiven Steuerung für Zerspanprozesse (Adapt-i-Cut) - Teilprojekt „Entwicklung der theoretischen Grundlagen zur Vorausberechnung der Zerspankräfte für die Optimierung einer CAM-Bahnplanung“
Die Kenntnis der Zerspankräfte und Lastverläufe ist äußerst aufschlussreich für den Prozessplaner, um bspw. kritische Stellen entlang des Werkzeugweges aufzuspüren. Neue analytische Zerspanmodelle ermöglichen eine rasche Zerspankraftberechnung entlang einer kompletten NC-Werkzeugbahn.
Moderne CAM-Systeme sind in der Lage, neben einer klassischen, vordefinierten Bahnaufteilung auch eine Werkzeugbahn auf Basis möglichst konstanter geometrischer Eingriffsbedingungen zu erzeugen. Trotz dieser Herangehensweise können wesentliche Änderungen der kinetischen Zerspancharakteristik an einzelnen Bahnsegmenten sowie Leerwege nicht immer vermieden werden. Dabei können Zerspankraftspitzen bis zu 70% über den nominalen Größen auftreten. Dies führt zu erhöhtem Werkzeugverschleiß, erhöhter Gefahr des Werkzeugbruchs und zur Beeinträchtigung der Genauigkeit und Qualität des zu bearbeitenden Bauteils sowie unter ungünstigen Umständen zu Prozessinstabilitäten.
Eine mögliche Verbesserung kann der Übergang von geometrisch konstanten zu kinetisch konstanten Eingriffsbedingungen zwischen Werkzeug und Werkstück eröffnen. Die Gewährleistung kinetisch konstanter Eingriffsbedingungen setzt allerdings die Vorab-Bestimmung der Zerspankraft in jedem Bahnpunkt voraus.
Im Rahmen des Projekts wird hierzu ein neuartiges, vollständig analytisches Zerspanmodell für den Fräsprozess entwickelt und implementiert. Der entscheidende Vorteil ist eine wesentlich allgemeingültigere Formulierung, die auch bei stark variierenden Eingriffsbedingungen und dynamisch veränderlichen Technologieparametern zu jedem Zeitpunkt eine gültige Zerspankraftprognose erlaubt – unter Verzicht auf aufwändige Versuchsreihen.
Dies ermöglicht in einem weiteren Integrationsschritt eine zusätzliche Abdrängungs- bzw. Nachgiebigkeitskompensation in Form eines ortsangepassten Bahnvorhalts bereits bei der NC-Programmierung im CAM-System. Insbesondere beim Einsatz langer, schlanker Werkzeuge wird auf diese Weise die Endkonturtreue und Genauigkeit wesentlich verbessert.
Gefördert durch: Zentrales Innovationsprogramm Mittelstand - ZIM
Im Forschungsvorhaben wurden Kreissägewerkzeuge auf ihre dynamischen und statischen Eigenschaften untersucht und Simulationsmodelle aufgebaut, um diese Eigenschaften abzubilden. Der Fokus der Untersuchungen lag dabei auf dem Einfluss der in Kreissägeblätter eingebrachten Laserornamente und deren Füllmaterialien, sowie der Flanschverbindung. Hierbei wurden die Einflüsse der maßgeblichen Parameter, wie der Oberflächenbeschaffenheit in der Fügestelle und der Anpresskraft, auf die Eigenschaften des Systems analysiert. Ausgehend von Modellversuchen zur isolierten Betrachtung der einzelnen Effekte wurde im Verlauf des Forschungsprojektes die Komplexität der Versuche und Simulationen schrittweise erhöht, um Wechselwirkungen der Einflussgrößen abbilden zu können. Die gesammelten Ergebnisse wurden auf das rotierende Gesamtmodell inklusive Aufspannung übertragen und experimentell validiert, um abschließend eine Sensitivitätsanalyse der Einflussparameter durchzuführen. Als Ergebnis der Analyse stellte sich heraus, dass im unbelasteten System weder der Mikroschlupf in der der Flanschschnittstelle, noch die Eigenschaften des Füllmaterials einen wesentlichen Einfluss auf das Systemverhalten ausüben. Die Gestalt und Anordnung der Schlitze und die durch den Flansch aufgebrachte Vorspannung ermöglichen jedoch eine deutliche Beeinflussung seiner statischen und dynamischen Eigenschaften.
Das Projekt wurde gemeinsam vom Institut für Werkzeugmaschinen (IfW) und dem Institut für Nichtlineare Mechanik (inm) der Universität Stuttgart bearbeitet.
Gefördert durch: DFG
Das Ziel des Forschungsprojektes war die Erhöhung des Prozessverständnisses bei der ultraschallunterstützen Zerspanung von Gestein mit geometrisch unbestimmten Werkzeugen. Dabei wurden prozessrelevante Einflussfaktoren und Wirkmechanismen, die noch nicht ausreichend beschrieben waren, untersucht. Wesentliche Erkenntnisse bezüglich der Prozessabläufe waren mittels linearer Ritzversuche mit einem einzelnen, an einem Ultraschallschwinger befestigten Diamantkorn möglich. Der Kontaktvorgang zwischen dem hochfrequent schwingenden Diamantkorn und senkrecht hierzu linear bewegten Gesteinsproben wurde mittels einer Hochgeschwindigkeitskamera visualisiert. Die Auswertung der Videoaufnahmen und Kraftverläufe zeigte bei schwingungs-überlagerter Prozessführung das Auftreten von Mikrohämmern und einen dreiphasigen Kontaktvorgang (Stoßkontakt, Eindringen und Separation). Darüber hinaus wurde ein Zusammenhang zwischen dem dominierenden Spanbildungsmechanismus und der Schnittgeschwindigkeit bei Schwingungsüberlagerung nachgewiesen. Während bei langsamen Schnittgeschwindigkeiten die Spanbildung infolge des Auftreffens der Dia-mantfreifläche auf die Probenoberfläche (Mikrohämmern und Sekundärspanbildung) entsteht, dominiert bei hohen Schnittgeschwindigkeiten die Spanbildung vor der Schneide (Primärspanbildung). Des Weiteren konnten in den schwingungsunterstützen Ritzversuchen zwei entgegengesetzt wirkende, Prozesskraft beeinflussende Mecha-nismen festgestellt werden. Einerseits führt eine Erhöhung der Schwingungsamplitude in der Kontaktzone zur Abnahme der Zerspankraft infolge der ansteigenden Schwingungsgeschwindigkeit und der damit verbundenen Reibungsreduktion. Gleichzeitig wirkt sich eine höhere Schwingungsamplitude auf die effektive Zustellung aus, wodurch der Spanungsquerschnitt zunimmt und die Zerspankraft steigt.
Der beschriebene Prozess wurde mit experimentell verifizierten Modellen beschrieben. Hierzu wurden Prozess und System in die Teilsysteme Werkzeug, Materialabtrag, Prozesskräfte, Kinematik und Ultraschallsystem aufgeteilt, separat modelliert und zu einem iterativen Gesamtmodell zusammengefügt. Das Ultraschallsystem wurde mit den be-rechneten Prozessbelastungen beaufschlagt und das daraus resultierende Schwingungsverhaltes des Systems ermittelt. Der jeweils nächste Iterationsschritt wurde mit den neu berechneten kinematischen Randbedingungen durchgeführt. Zur Kopplung der Teilmodelle wurde ein generisches Framework entwickelt, mit dem unterschiedlichste und beliebig viele Teilmodelle verbunden werden können. Das erstellte Gesamtmodell stellt ein nutzbares Werkzeug zur Auslegung der Systemkomponenten dar.
Mittels modellgestützter Parameterstudien wurde die Lagerung des Ultraschallschwingers als wesentlich für das Schwingverhalten unter Last identifiziert. Eine dementsprechend optimierte Schwinger-Werkzeugkombination wurde mittels des Gesamtmodells und eines Optimierungsalgorithmus bestimmt und anschließend aufgebaut. Mit beiden Schwingungsgebilden wurden Bohr- und Fräsuntersuchungen durchgeführt. Das optimierte System zeigte eine höhere Prozesskraftreduktion (68-90 %) als das Ausgangs-system (41-80 %). Darüber hinaus zeigte sich das optimierte Schwingungsgebilde robuster gegenüber der Änderung von Prozessgrößen. Auch bezüglich der elektrischen Leistung wies das optimierte System ein verbessertes Verhalten auf.
Gefördert durch: DFG
Kontakt
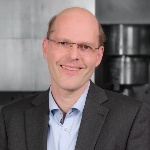
Rocco Eisseler
Dr.-Ing. Dipl.-Gwl.Gruppenleiter Zerspanungstechnologie