Research projects of Wood and Composites Machining
Determination of balancing strategies and technically reasonable balance qualities with regard to the machine dynamics for tools in wood machining
The unbalance condition of high-speed tools and its effect on the machining quality, the cutting edge wear and the spindle bearing load can only be determined by taking account of the system out of tool, tool holder and spindle. Interfaces here have a considerable influence on the actual unbalance condition of the tool in the machine, so that even precisely balanced tools in machines can cause quite detrimental bearing loads or poor machining qualities due to so-called component unbalances.
The goal of this research project is to carry out methodical analyses for establishing the achievable balance quality for woodworking tools. For that reason, it is intended to develop a completely new approach to limit the vibrations in the machine structure caused by unbalances. The dynamic vibration behaviour of the machines in question serves as a basis here. Limiting values for unbalance-induced vibrations are to be derived for reference machines, depending on the rotational frequency, unbalance force and dynamic stiffness of the machine.
The loads of the spindle bearings as well as machine vibrations can be limited by directly detecting the unbalance condition of the tool by means of the machine vibrations and correspondingly adapted measures (e.g. reduction or increase in rotational speed or resetting of tools). It is intended to develop approaches for that, in order to conclude unbalance-induced tool eccentricities from acceleration signals at relevant points of the respective machine structure. Then measures could be taken, such as a specific adaptation of rotational speed to more stable operating points of the machine or a reorientating of the tool. In addition, balancing strategies are to be developed based on statistical models with which it is possible to establish the influence of the tool’s interface tolerances as well as of the interfaces (e.g. hollow shaft taper, coupling plug).
Funded by
German Federation of Industrial Research Associations (AiF) within the programme for collective Industrial Research (IGF) from funds of the Federal Ministry for Economic Affairs and Energy by order of the German Bundestag
Production and joining optimization for multi-storey exterior walls made of squared solid timber with slots
The enormous challenge facing the building and construction industry is how to reduce the consumption of resources, emissions and pollution in all areas of the process chain from raw materials production, the use in the building up to the recycling at the end of the life cycle. As wood is a renewable, local building material, it offers very good prerequisites for an efficient and energy-saving use of resources.
In the predecessor project, a novel wooden construction was developed only consisting of squared solid timber as supporting and insulating material. Thus, it is only made of wooden components and joints, requiring no adhesives for joining as well as no additional insulation. To evaluate the system, a full-scale microhouse (IBA Timber Prototype House) was realized successfully for the International Building Exhibition (IBA) Thüringen.
The intention here is to make these characteristics applicable to multi-storey residential and office buildings within an optimized system. By further developing the profile of the squared solid timber and the prototypical machining process into a production process applicable in industry, it is intended to increase both the production efficiency and the airtightness of the component layers.
In the joint project "Economical, high-insulation, layer-reduced, mono-material, adhesive-free, digitally produced solid timber construction" with the Institute for Computational Design and Construction (ICD) at the University of Stuttgart, the task of the IfW is to optimize the production of the wooden elements. The goal of the production optimization is to contribute to realizing the high-performance cutting of solid timber by means of machining centres. The centre of attention here is on the integral complex out of „workpiece, tool and production process parameters“, looking at it from the aspects of process effectiveness. By conducting experimental cutting tests, it is planned to obtain findings about process parameters as well as tool characteristics and to take them into account in the design of an optimum machining strategy.
Funded by the Federal Ministry of the Interior, Building and Community (BMI) within the research funding “Zukunft Bau“.
Implementation of an IoT platform for digitalizing the machine hall for wood machining
The progressive digitalization and automation in industry offer versatile, new possibilities for networked and intelligent machining. For that purpose, the machining centres at the IfW were made fit by means of an IoT platform for a SmartLab („digital wood laboratory“) in the course of a trilateral „Industry 4.0“ project. This enables the merging of diverse data sets, which can be connected with each other by means of intelligent analytical methods. Thus it is possible to draw conclusions about the respective machine conditions and hence about the production process as well as to derive predictions. This transformation is based on the cloud-based technology platform by Tapio and the central data acquisition unit by Schneider Electric SE.
In order to further digitalize the machine hall at the IfW, a central data acquisition unit was installed to collect the data of several measurement stations, process them and make them visible via different output mediums. For that purpose, a sensor system was implemented to establish the climate data in the machine hall and control the limiting values so that it is possible to monitor environmental influences on machines and facilities. The energy consumption of the central wood chip and dust extraction system as well as of the CNC machining centres is measured by means of wattmeters so that conclusions about the utilization can be drawn. This is necessary because there is no other way of measuring the power consumption of the present machines. The present machines were connected to the IoT according to the BrownField approach.
The machine and sensor data are recorded here in the form of OPC UA items by an OPC UA server so that they can be read out by a cloud connector. It forwards these data to the digital ecosystem, which makes them available for various applications. The MachineBoard, an application by Tapio, was used exemplary in the SmartLab. The MachineBoard runs as an app on mobile terminals (smartphones, tablets, smartwatches, etc.) and visualizes the information about the machining centres and the machine hall.
The special quality of the solution realized at the IfW is that the machines and facilities already implemented can be supplemented not only by numerous other machines and test stands in the machine hall but also by further sensor and actuator systems. Thus it is possible to flexibly adjust and expand the digitalization of the machine hall to the changing requirements, e.g. in test procedures. For any application, it is possible to choose sensors or read data directly out of the machine. In contrast to industrial production, the project described here is not focused on increasing the productivity but on establishing basic data, such as e.g. the spindle utilization, the variance in rotational speed, the machine condition, etc. Moreover, the centre of attention here is on the testing of the IoT platform and the generation of new knowledge, from which industrial production can derive benefit in turn.
We are grateful to Tapio and Schneider Electric SE for their previous and continuing support in the realization of the BrownField approach for digitalizing the machine hall at the IfW.
Development of adaptive and shape-flexible extraction hood systems for effectively collecting chips and dust in the machining of wood and composites
The requirements on the production of components out of wood and composites are increasing constantly. For an efficient machining, the machines and systems have to be flexibly adaptable to diverse workpiece variants, even if the lot sizes are often small. The individuality of workpieces is, however, inconsistent with a high productivity due to the increasing resetting time. The machining of wood and composites is often accompanied by great emissions of chips and dust. Owing to cost and performance pressure, better drive and control systems of machine tools as well as more effective production strategies, the cutting capacity is increased leading to larger amounts of chips as well. Chips and dust do not only impair the health of machine operators but also machines and workpieces. Thus workpieces cannot reach the required manufacturing quality, and machines have a shorter service life as well as a lower productivity. Hence, it is necessary to effectively collect and remove the dust and the chips arising in machines. Chip collection depends decisively on which extraction hood is used.
The extraction hoods used in production cannot be adapted to rapidly changing tool and workpiece geometries as well as production processes, resulting in an insufficient chip collection. This is increased by the also varying composition and shape of the arising dust and chip flow as well as its distribution in the working space of a machine. Up to now, this problem has been counteracted by working with very large extraction volume flows and extraction capacities. The chips still remaining in a machine or on workpieces must be removed, requiring a lot of money and time. Additional tool wear due to „double cutting processes“, the cleaning or deterioration of workpieces lead to further expenditure or rejects, increasing the production costs and decreasing productivity.
In order to resolve these technical and economic problems, new extraction hood concepts are being developed and tested together with the IWF Braunschweig. On the one hand, a quick setting-up and adaptation is achieved by means of a shape-flexible extraction hood which can be adjusted and reshaped by hand. On the other hand, an active extraction hood which consists of several parts and can be adjusted to the chip flow by means of actuators is being built and examined.
Funded by: German Federation of Industrial Research Associations (AiF) within the programme for Collective Industrial Research (IGF) from funds of the Federal Ministry for Economic Affairs and Energy by order of the German Bundestag
Increasing the efficiency of chip collection in the machining of composite and wood-based materials as well as plastics
With an average of 45 %, the extraction system requires the greatest amount of electric energy in a woodworking company. In the past, attention was primarily focused on increasing the capture efficiency, in order to comply with the legal limiting values. Today, energy efficiency is being given more and more priority in production.
The fundamental goal of this research project is to clearly reduce the energy required by the extraction systems of machines for the machining of wood as well as fibre composite materials and plastics. Two ways are chosen for increasing the energy efficiency of extraction systems:
- self-regulating, decentralized extraction systems
- chip collection devices close to the tool
The intention here is to combine both approaches to an energy-efficient collection of dust and chips in cutting machine tools.
In the context of the research project, a sample process or rather sample workpiece was developed to assess the capture efficiency for CNC machining centres. Tests with the sample workpiece showed that the capture efficiency depends not only on the air speed inside the hood but also on the size distribution of the chip and dust particles.
Funded by: German Federation of Industrial Research Associations (AiF) within the programme for Collective Industrial Research (IGF) from funds of the Federal Ministry for Economic Affairs and Energy by order of the German Bundestag
Low-noise circular saw blades in the machining of wood and wood-based materials
Noise continues to be one of the most common health hazards in the wood machining industry. The noise level of circular saws is almost always at or above the permissible noise limit values. However, the strategies, which have been pursued until now to reduce acoustic emissions, change the acoustic behaviour of a circular saw blade only insignificantly. This is because they rather fight against the effects than against the mechanism of sound generation in the case of rotating circular saw blades.
The IfW has carried out tests showing that current circular saw blades have an oversized chip space to guarantee a reliable chip removal during cutting in any event. The research work is laid out to analyse design changes to the geometry of saw blade body and tooth shape, which cause less air turbulences, e.g. due to a reduction and optimization of the chip spaces. The focus here is on examining how different geometry parameters, such as e.g. tooth back length, tooth shape or chip space radius, influence the acoustic behaviour of a circular saw blade. This is aimed at influencing the flow behaviour by means of suitable measures regarding the design of the circular saw blade, so as to reduce the acoustic emissions without essentially impairing the machining capability of the circular saw blade. The basis for that is to be provided by experimental cutting tests, acoustic measurement analyses as well as aeroacoustic simulations.
Funded by: German Research Foundation (DFG)
Increasing the occupational safety of stationary woodworking machines by means of machine enclosures out of plastics and fibre composites
The trend towards complete machining through process integration causes an increasing demand for further additional units for woodworking machines. As a result, the machine enclosures of machining centres are becoming bigger and bigger in order to be able to house the large number of units. Moreover, it is inevitable that these units lead to an increase of the masses to be moved. In order to counteract this trend, it becomes interesting to use lightweight materials for machine enclosures. These materials are, however, not covered in the current standard EN 848-3 for the retention capacity.
The aim of this research project is to find suitable lightweight materials which could be used for making safeguards as an alternative to existing solutions, mostly made of sheet steel. For that purpose, the safety characteristics (e.g. retention capacity) of these weight-reduced materials have to be established. In addition, it is also intended to improve the acoustic behaviour by means of the new material, because the machine enclosure screens the prominent sound sources (spindle, cutting zone).
By systematically examining and establishing alternative enclosure materials, it will become possible to use these materials already in the design phase, without additional extensive and expensive safety tests by the manufacturers later. This will show and document the great economic and ecological advantages over existing solutions.
Funded by: German Federation of Industrial Research Associations (AiF) within the programme for Collective Industrial Research (IGF) from funds of the Federal Ministry for Economic Affairs and Energy by order of the German Bundestag
Development of heavy-duty lightweight tool bodies for the machining of wood and wood-based materials
The trend towards higher and higher cutting speeds in the machining of wood and wood-based materials requires increasingly higher rotational speeds or bigger building tools. The increase in geometrical dimensions is always accompanied here by a greater mass of the tools. This is directly related to the dynamic behaviour of the machine tool and the tool spindle. Regarding moving axes (e.g. in CNC machines for ultraprecision cutting), there are sometimes great acceleration forces due to the heavy tools. In addition, the critical rotational speeds of spindles decrease due to heavy tools, thus limiting the maximum rotational speeds.
To fulfil the trend towards higher and higher rotational speeds, this research project deals with the development of a tool body built of carbon fibre composite. This material is characterized by excellent specific stiffness and damping characteristics, as required for the use of tools in wood machining. To apply these advantages to tools, solutions are being worked out within the IGF project 20128N „Development of heavy-duty lightweight tool bodies for the machining of wood and wood-based materials“, funded by the Federal Ministry for Economic Affairs and Energy (BMWi). As an example, a prototype tool with lightweight body for planing processes is to be developed in the project. This precompetitive development work is orientated towards working out solutions to suitable production processes for the body and its connection to cutting and interface elements.
The German Institutes of Textile and Fiber Research (DITF) carry out the operational development of prototypes for tool bodies designed with respect to load, whereas the Institute for Machine Tools (IfW) conducts the developments and investigations regarding the tool. The project is meant to gain findings regarding the suitability of fundamental processes and concepts for producing tools with bodies out of fibre composite, which can subsequently be realized by the members of the working group from industry. As there are mainly small and medium-sized enterprises in the textile-working as well as in the wood machining industry, new markets will be opened up for all parties involved. In addition, the efficiency of tools for wood machining will be increased thanks to lighter tools so that technological leads can be secured.
Funded by: German Federation of Industrial Research Associations (AiF) within the programme for Collective Industrial Research (IGF) from funds of the Federal Ministry for Economic Affairs and Energy by order of the German Bundestag
Simplified robotic woodwork (SiRoWo)
The use of industrial robots in production is spreading more and more. The centre of attention here is mainly on the automation of complex assembly and joining processes. In a few cases, robots are also used directly for production processes like milling and drilling nowadays. It has shown, however, that it is very complex and time-consuming to set up and program these processes in the control of a robot. That is why robots are currently used only marginally for these purposes. Moreover, it has shown primarily in metalworking that the stiffness of the robot kinematics is often not sufficient for these processes or rather that the arising machining forces are too great. In the machining of wood and materials similar to wood such as e.g. fibre composite materials and plastics, the kinematic stiffness of a robot is, however, often sufficient as the required machining forces are lower. These applications are rather focused on the flexible adaptation to complex components with various machining processes. The paramount goal of the total project is to build and commission a prototype machining cell with industrial robots which makes it possible to fully automatically produce complex components out of wood or materials similar to wood. This includes the approach to realize a simple and user-friendly programming environment.
The IfW is working here on the subproject „Development and integration of strategies for the machining of wood and composite materials with robots and an extraction device for a fully integrated robot machining cell”. The goal of this subproject is to create the technological requirements for the different machining processes of wood and composite materials and to develop the necessary peripherals for removing chips and dust as well as for clamping the workpieces. Within the framework of this subproject, the considered machining processes are to be adapted to the kinematic conditions of an industrial robot. Moreover, the knowledge required for an intelligent continuous-path planning of robot motions and the necessary indicators of process monitoring are to be established by means of experimental analyses and then supplied to the project partners.
Funded by the funding initiative „KMU-NetC“ from funds of the Federal Ministry of Education and Research by order of the German Bundestag
Comparison and further development of methods for measuring wood dust emissions as well as examination of their practical application
Within a bilateral research project of the Social Accident Insurance Institution for the Woodworking and Metalworking Industries (BGHM) and the Institute for Machine Tools, measuring methods were examined for establishing and evaluating wood dust emissions of machining centres. The focus here was on gravimetric analyses, the tracer method, the method of weight comparison as well as an alternative method with low-cost sensors.
The machining of solid wood and wood-based materials is accompanied by great emissions of chips and dust. Wood dust is harmful to health and carcinogenic. According to TRGS 906, it is classified as K1A/K1B or K2 depending on the type of wood. Apart from the health hazards described here, there are further risks, such as e.g. danger of fire and explosion, when working with wood dust or when wood dust is arising. Yet, these dangers are not the subject of this research.
An effective concept for collection and extraction is required to reduce the exposure of workers. It can be assumed that an effective reduction in emissions has a favourable influence on the exposure at work as well. However, a quantitative correlation has not been proved until now. In addition, the deposition of chips and dust leads to a greater cutting edge wear, a worse machining quality and to necessary subsequent work steps in the production process, such as e.g. a manual dedusting of the workpieces.
To assess the machine emissions more easily, it makes sense to compare the methods for measuring emissions. At the moment, hardly any manufacturer examines the emissions of machines as the measurement requires a lot of time, the necessary measuring instruments are not available and the staff has insufficient knowledge of the tests. To evaluate the measuring methods, not only the expenditure required for conducting a measurement was analysed but also the meaningfulness of the measuring results. The findings of the research project are meant to assist the machine manufacturers with evaluating the risk of their machines‘ emissions.
The investigations were carried out with a project funded by the Social Accident Insurance Institution for the Woodworking and Metalworking Industries (BGHM).
Contact

Kamil Güzel
Dipl.-Ing.Team leader Wood Machining
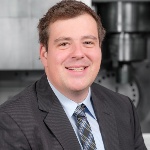
Matthias Schneider
Dipl.-Ing.Team leader Composite Materials Machining