Research projects of Machine Analysis
Component-related machine configuration in production through additional cyber-physical modules (BaZMod)
Within the BaZMod project, a new „intelligent“ interface at the flat contact surface between spindle and hollow shaft taper was developed to transmit energy and data. It was realized by means of eight spring-loaded tool contact pins and eight spindle contact surfaces. Numerous electric, mechanical and thermal tests were carried out to examine the transmission quality and the endurance limit of the contacts under different environmental conditions.
First, the insulation quality of the contacting was analysed for dry contact areas and wet contact areas with coolant in the case of different test voltages (100 V, 500 V and 1.000 V). The insulation resistance Riso was used to assess the insulation quality. It was detected that the insulation quality is sufficiently high for both dry and wet environmental conditions. In addition, the data transmission behaviour of the contacting was examined on the basis of different signal types. It was found to be almost unvarying for all signal types.
Moreover, the endurance limit of the contacting was analysed. For that purpose, 100,000 cycles were run with a suitable test stand, at which the interface was opened and closed. In the evaluation, it was detected that a slight to moderate track was formed at the insulation surface of the spindle owing to the material removal of the opposite seal. Several times, a pin got stuck at the tool. In order to eliminate these problems, the seals and installation tolerances are being optimized at the moment.
In addition, the thermal behaviour of the contacting to the spindle nose was analysed at a maximum electric load (ca. 600 W) and at different environmental conditions (dry, coolant and oil). No dependence on the environmental conditions was found. As the contact zone had a temperature of about 45 °C, its warming was harmless.
Until the end of the project, the research subject by the IfW will be to carry out further series of tests on the endurance limit of the optimized contacting as well as to analyse the dynamic behaviour of the BaZMod spindle in comparison with a conventional spindle. Currently, the machine prototype SW BA422 with hollow shaft taper HSK-i is in the machine hall of the IfW.
Funded by: Federal Ministry of Education and Research
Development of an adaptive control (Adapt-i-Cut) – Subproject: „Development of the theoretical basis for predicting the resultant forces to optimize a CAM path planning“
For the process planner, it is extremely informative to know the resultant forces and the load curves, for example, in order to detect critical areas along the tool path. New analytical cutting models make it possible to quickly calculate the resultant forces along a complete NC tool path.
Modern CAM systems are capable of creating not only a classic, predefined path layout but also a tool path on the basis of geometrical engagement conditions that are as constant as possible. Despite of this approach, it is not always possible to avoid substantial alterations in the kinetic cutting characteristics of individual path segments as well as idle travel. There may be peak resultant forces of up to 70% in relation to the nominal values. This leads to an increased tool wear and risk of tool breakage, a reduced accuracy and quality of the machined component as well as to unstable processes in unfavourable circumstances.
A possible improvement may be to change from geometrically to kinetically constant engagement conditions between tool and workpiece. However, a guarantee of kinetically constant engagement conditions requires to determine the resultant force for each path point in advance.
For that purpose, a novel, completely analytical cutting model for milling processes was developed and implemented in this project. The crucial advantage here is an essentially more general modelling, allowing a valid prediction of resultant forces at any time even in the case of greatly varying engagement conditions and dynamically variable technology parameters – without time-consuming series of tests.
In a further integration step, this makes it possible to additionally compensate the deflection and compliance in the form of a location-adapted derivative path action already during the NC programming in the CAM system. In this way, it is possible to considerably improve the net shape and accuracy, especially when using long, slim tools.
Funded by: Central Innovation Programme for small and medium-sized enterprises - ZIM/AiF
Acoustic fingerprints – Development of a system to monitor and diagnose milling processes through an online analysis of acoustic fingerprints
In this project, it is intended to develop for the first time an economical prototype bundle of software and hardware for process monitoring based on the airborne sound radiation of a running process in the working space of machine tools. The system should make it possible to monitor large-scale processes on the basis of a fingerprint from a process sequence with good parts. The evaluation is meant to produce not only a pure time-frequency analysis but also a reference to the area of the workpiece and to the spindle angle. The core technologies here are self-learning adaptive nonlinear models for detecting process deviations and for identifying causes. As further subjects of development, it is not only planned to realize a practical arrangement of the measuring system as well as an optimum integration and positioning of the microphones in the working space but also the effective suppression of interfering ambient noises by using the lock-in technique. It is particularly challenging here that the system with all its analytical algorithms has to be real-time capable. The real-time capability of the complete system and its analytical algorithms is to be guaranteed by a special hardware platform (dSPACE) for the prototype.
An easy, economical and permanently fail-safe implementation is impeded by the rough process conditions in the working space of cutting machine tools with chip production, dusts, coolant application, vibrations and thermally loading environmental conditions as well as by a time-consuming and expensive signal transmission when using sensors in rotating tools or workpieces and devices. Systems based on complex sensor technology do not necessarily improve the overall reliability and availability of a machine system, since the total complexity is higher and the systems themselves have a certain probability of failure.
Using the airborne sound emissions radiated by the process into the working space of the machine tool as monitoring signal offers considerable implementation and cost advantages here. By installing economical and robust microphones at a sheltered place in the working space, it is possible to avoid the above-mentioned disadvantages of common signal acquisition systems today. At present, an intelligent process monitoring of milling operations based on their airborne sound radiation is not available as real-time application on the market.
Funded by: AiF / ZIM
Contact
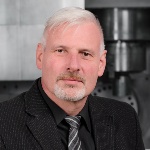
Steffen Braun
Dipl.-Ing.Team leader Machine Analysis