Research projects of Machine Design
Supported by the state of Baden-Württemberg, the Karlsruhe Institute of Technology (KIT) and the University of Stuttgart have launched a 3D printing cloud for the first time
Additive manufacturing offers great potential to research and industry: low costs, shorter production times, flexible and customer-orientated production. It will become of even greater importance in future as the demand for individualized products is growing. Researchers of the German Academic Association for Production Technology (WGP) have created a cloud containing all components of a complete process chain for additive manufacturing. Companies wishing to manufacture a part additively can find here all sub-modules necessary for its production and put them together individually.
Compared with previous technologies, additive manufacturing processes can produce very complicated parts in a clearly more economical way in smaller numbers of pieces with shorter lead times in smaller numbers of pieces. Due to the additional degrees of design freedom, it is moreover possible to manufacture component structures which could be produced only in a very time-consuming and cost-intensive way up to now, if at all.
Within the project called „3D printing cloud BW“, the Institute of Production Science (wbk) at the Karlsruhe Institute of Technology (KIT) and the Institute for Machine Tools (IfW) at the University of Stuttgart are creating an open online platform for the entire process chain of additive manufacturing.
By the year 2020, this platform is meant to concentrate the multiple current and future special processes developed by universities and enterprises in Baden-Württemberg, to link players and offer their processes and technologies as industrial services to interested customers. Thus by means of the 3D printing cloud BW, it will not only be possible to generate orders which cannot be carried out so far but also to process them in a rather easy way.
Funded by the Baden-Württemberg Ministry of Science, Research and Arts
Development of a process model for simulating adaptive control concepts for metal-cutting bandsawing
In the first funding period of this project, a process model was developed with the simulation environment MATLAB/Simulink based on analyses and experiments of the bandsawing process. Extensive experimental analyses were carried out here with a test machine as well as in model tests like the developed single-tooth sawing test. This was supported by extensive static and dynamic FE simulations making it possible to take a detailed account of the individual aspects regarding the factors influencing the bandsawing process. A large part of the experimental work was concerned with examining the deflection of the saw band and correlating it with the passive force. In this way it was possible to understand the total process more thoroughly. Finally, adaptive control concepts were taken into account with which the bandsawing process can be optimized by specifically influencing the dynamic properties, in order to anticipate what is planned in the second project period. The results obtained in the first project period until now showed the potentials for optimizing the bandsawing process in order to increase the productivity by reducing tool wear. An additional positive effect of this is the resultant improvement of the workpiece surface. This approach to examine and discover optimization potentials with the developed process model can be considered as a practical solution for reducing the time needed for experiments and analyses with regard to the process design.
Hence, it is planned in the second project period to apply the innovative process model for the simulation of adaptive control concepts for metal-cutting bandsawing and then implement an adaptive control in the test band saw on the basis of the results gained. Finally, it is intended to show the optimization potentials of the adaptive control on the bandsawing process by means of experiments.
Funded by: German Research Foundation (DFG)
Within the framework of a BMWi-funded (Federal Ministry for Economic Affairs and Energy) cooperation project with EMO Systems from Berlin, a trouble-free multi-axis force measuring device was developed for detecting process forces in machine tools.
The developed prototype of a force measuring platform based on strain gauges enables a quick high-precision measurement of process forces and moments in six axes. The multi-redundant detection of the measured values for all force components leads to an increase in resolution and sensitivity, which has been unattained so far for strain gauge systems. The developed force measuring platform can be applied to process diagnosis, process control and process stability.
An integrated highly sensitive disturbance variable sensor makes it possible to compensate inclinations, accelerations and vibrations. The disturbance variable sensor provides the same sensitivity and measuring data ratio as the force measuring platform itself. The relevance of this technology is worth mentioning as the disturbance variable sensor can be adjusted to the properties of the force measuring platform with regard to sensitivity, resolution, measuring data ratio, zero-point stability and natural frequency. Moreover, it can be configured in the same way and optimally synchronized with the other sensors of the force measuring platform.
The software developed within the project provides extensive possibilities for configuration, representation, analysis and storage as well as a reliable disturbance-variables compensation of vibrations, accelerations and inclinations in real time.
The fundamental challenges of this project were to detect the temperature-related disturbances and to minimize their influences through an active temperature control. The greatest zero-point stability was attained by cooled sensors for measurements over longer periods of time so that the thermal response time could be clearly reduced. Further development goals were to achieve the greatest possible stiffness in the interest of a high natural frequency without making a compromise on sensitivity.
Funded by: Central Innovation Programme for small and medium-sized enterprises - ZIM
Simplified Robotic Woodworking (SiRoWo)
The use of industrial robots (IRs) for machining tasks is becoming more and more widespread in production. The reason for this is that an IR has a wide operating range at comparatively low investment costs compared with machine tools. In the machining of metallic materials, it has shown, however, that IRs often cannot achieve the close manufacturing tolerances in metalworking due to their great dynamic compliance. This situation is clearly better in the machining of non-metallic materials such as wood and fibre composite materials, since the specific forces are lower and the manufacturing tolerances are greater. For that reason, IRs are predestined for many fields of application in the woodworking industry.
It is necessary to develop a hardware concept suitable for everyone so that IRs can be widely applied in the trade. This requires a programming environment which is orientated towards various tasks of a workshop and can be operated intuitively. A database is also planned to help with supplying operations and production steps, sketches, industrial design and material requirements with few clicks. Apart from software-related problems, the project is also focused on the development of hardware components such as clamping and suction.
The IfW is working on the subproject „Development and integration of strategies for the machining of wood and composite materials with robots and a suction device for a fully integrated robot machining cell”. The goal of this subproject is to create the technological requirements for the different machining processes of wood and composite materials and to develop the necessary peripherals for removing chips and dust as well as for clamping the workpieces. Within the framework of this subproject, the considered machining processes are to be adapted to the kinematic conditions of an industrial robot. Moreover, the knowledge required for an intelligent continuous-path planning of robot motions and the necessary indicators of process monitoring are to be established by means of experimental analyses and then supplied to the project partners.
Funded by the funding initiative „KMU-NetC“ from funds of the Federal Ministry of Education and Research by order of the German Bundestag
Development of a vibration-reduced lightweight milling cutter in multimaterial design
This cooperation project is concerned with developing a milling cutter with great cantilever length in multimaterial design. For the first time, it is dared to venture away from a milling base made out of high-quality metal towards a combination of different manufacturing processes and various materials. A main goal here is a lightweight design in order to reduce moving masses, improve the energy efficiency and adapt efficient tools to selected production conditions. On top of that, the tendency to chattering is to be clearly reduced for these tools with great cantilever length.
In the course of developing the lightweight milling cutter, the percentage of metallic materials is to be minimized and replaced with lighter plastic materials by means of optimizing the force path and the topology. Based on the positive experiences of selective laser melting, it is planned to additively manufacture metallic skeletal structures of the tool and join them by filling their damping structure with high-performance plastic elements.
By applying the new manufacturing methods, it is intended to develop and model the tools with channels for coolant and electric cables to sensors as well as with chip cleaning segments and forms, which could not be produced until now with conventional manufacturing methods.
Funded by: Central Innovation Programme for small and medium-sized enterprises (ZIM) of the Federal Ministry for Economic Affairs and Energy (BMWi)
This research project was aimed at developing a method for optimizing the design of a workholding fixture by means of artificial intelligence. The machining accuracy, efficiency and reliability of workholding fixtures depend on the number and the configuration of clamping and supporting devices. In the machining of filigree and thin-walled workpieces, there are often defects as a result of elastic deformations or regenerative chattering. This can restrict the machining accuracy and may even damage or destroy components.
An automated solution to the clamping problem presented was approximated by means of a regression method from the field of machine learning. First, an FE simulation was carried out to generate representative snapshots of the input and output data, which were used as training data for programmed regression models. Then various regression algorithms were conceptually analysed regarding their suitability for the underlying database. Finally, it was examined how the clamping principle influences the workpiece dynamics and the machining process for thin-walled components.
This subproject is a supplementary programme of a PhD thesis at the Graduate School of Excellence advanced Manufacturing Engineering and is funded by the Baden-Württemberg Ministry of Science, Research and Arts.
In order to optimize the coherence of an innovative teacher training at vocational schools, the LEBUS² project (Teacher training at vocational schools 2 in the framework of the quality initiative for teacher training) is aimed at linking subject science to subject didactics. Within the subproject conducted by the IfW, it is intended to develop and test a programme for the subject course „Mechatronics of machine tools“.
Representing a mechatronic multitasking system of a machine tool, the complex turning/milling centre Index R200 will be didactically used as demonstration model as well as virtual machine by means of AR/VR methods. Inquiring learning or rather the use of complex technical experiments is meant to take place by establishing the fields of application and the characteristics of various drive concepts or types of motors in machine tools. In addition, the focus is on creating CNC programs for cubic and rotative workpieces on SinuTrain terminals as well as on real machine tools. Further mechatronic competences will be worked out with a multi-media training system.
The subproject to LEBUS² is carried out together with the Institute of Educational Science (IfE), Department of Vocational Education focused on Teaching Technology (BPT), Professor Zinn.
The project „Teacher training at vocational schools in the framework of the quality initiative for teacher training“ is supported with federal and state funds by the Federal Ministry of Education and Research.
Within a research project with industry cooperation, a smart milling tool with indexable inserts was developed together with Avantec Zerspanwerkzeuge from Illingen. The cyber-physical system consisted of a milling tool in the form of a redesigned inserted-tooth cutter with electronics on a specially developed PCB (printed circuit board) with microcontroller, various sensors, data storage and transmission unit as well as accumulator.
The goal of the system development was to increase reliability as well as tool life and save costs due to a continuous predictive analysis of the milling process. By means of continuously measuring the physical parameters, cutting force and temperature of every cutting edge as well as the motion/vibration during the machining process, it was possible to detect the wear condition of the indexable inserts due to an intelligent assessment of the data.
The data collected can be stored in the tool and simultaneously be made available to an evaluation station by Bluetooth and from there to the end user on his smartphone, tablet, etc. After training the milling process, the end user obtains a push message as soon as the process has reached a critical condition or the indexable insert is at the end of its service life and must be replaced or turned.
Funded by: Central Innovation Programme for small and medium-sized enterprises (ZIM) of the Federal Ministry for Economic Affairs and Energy (BMWi)
Contact
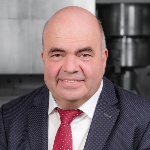
Walther Maier
Dipl.-Ing.Team leader Machine Design